Study Notes
Operational Objectives
- Level:
- AS, A-Level
- Board:
- AQA, Edexcel, OCR, IB
Last updated 22 Mar 2021
The operations function of a business is the "engine-room" of the business, and like all engines, performance can and should be measured.
All business operations of whatever size and complexity should have objectives set. The key objectives for operations are outlined below.
Cost & volume targets
However it chooses to compete, a business needs to ensure that operations are cost-effective.
The traditional measure of cost-effectiveness is "unit cost" – the average cost of producing a unit of the product. Businesses competing in the same industry face similar cost structures, but each will vary in terms of its productivity, efficiency and scale of production. The business with the lowest unit cost is in a strong position to be able to compete by being able to offer the lowest price, or make the highest profit margin at the average industry price.
Objectives relating to cost and volume tend to focus on:
- Productivity & efficiency (e.g. units per week or employee)
- Unit costs per item
- Contribution per unit
- Number of items to produce (per time period, or per machine etc)
Quality targets
Achieving or exceeding the required level of quality is also essential for a successful business.
There are many ways of measuring the achievement of "quality", including:
- Scrap / defect rates: a measure of poor quality
- Reliability – how often something goes wrong; average lifetime use etc
- Customer satisfaction – measured by customer research
- Number / incidence of customer complaints
- Customer loyalty – e.g. percentage of repeat business
Efficiency and flexibility targets
Closely linked to cost, efficiency and flexibility targets look at how effectively the assets of the business are being utilised, and how responsive the business can be to short-term or unexpected changes in demand. Efficiency and flexibility are key drivers of unit costs. Relevant objectives would include:
- Labour productivity: e.g. output per employee, units produced per production line; sales per shop
- Output per time period: e.g. potential output per week on a normal shift basis; potential output assuming certain levels of capacity utilisation
- Capacity utilisation: the proportion of potential output actually being achieved
- Order lead times: e.g. the time taken between receiving and processing an order
Environmental targets
This is an increasingly important focus of operational targets as businesses face more stringent environmental legislation and consumers increasingly base their buying decisions on firms that take environmental responsibility seriously. Examples include:
- Use of energy
- Proportion of production materials that are recycled
- Compliance with waste disposal regulations / proportion of waste to landfill
- Supplies of raw materials from sustainable sources
You might also like
Workforce Effectiveness & Management (Revision Presentation)
Teaching PowerPoints
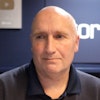
Improving Labour Productivity and Quality - A Shorter Working Week?
17th September 2015
The Jelly Bean Factory and the Productivity Puzzle
20th June 2016
Short-termism
Study Notes
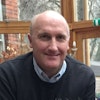
Quality in Business - Key Topic Revision for 2018
1st June 2018
Daily Email Updates
Subscribe to our daily digest and get the day’s content delivered fresh to your inbox every morning at 7am.
Signup for emails