Study Notes
Kaizen
- Level:
- AS, A-Level
- Board:
- AQA, Edexcel, OCR, IB
Last updated 22 Mar 2021
Kaizen (or ‘continuous improvement’) is an approach of constantly introducing small incremental changes in a business in order to improve quality and/or efficiency.
This approach assumes that employees are the best people to identify room for improvement, since they see the processes in action all the time. A firm that uses this approach therefore has to have a culture that encourages and rewards employees for their contribution to the process.
Kaizen can operate at the level of an individual, or through Kaizen Groups or Quality Circles which are groups specifically brought together to identify potential improvements. This approach would also be compatible with Team working or Cell Production, as improvements could form an important part of the team’s aims.
The key features of Kaizen include:
- Improvements are based on many, small changes rather than the radical changes that might arise from Research and Development
- As the ideas come from the workers themselves, they are less likely to be radically different, and therefore easier to implement
- Small improvements are less likely to require major capital investment than major process changes
- The ideas come from the talents of the existing workforce, as opposed to using R&D, consultants or equipment – any of which could be very expensive
- All employees should continually be seeking ways to improve their own performance
- It helps encourage workers to take ownership for their work, and can help reinforce team working, thereby improving worker motivation
As Kaizen is characterised by many, small improvements over time, it contrasts with the major leaps seen in industry when radical new technology or production methods have been introduced. Over the years, the sheer volume of Kaizen improvements can lead to major advances for a firm, but managers cannot afford to overlook the need for radical change from time to time. For example, many UK manufacturers and service companies have found it necessary to outsource processes to cheaper centres such as India and China – these changes would be unlikely to arise from Kaizen.
Whilst staff suggestions can help to enrich the work for many employees, Kaizen can be seen as an unrelenting process. Some firms set targets for individuals or for teams to come up with a minimum number of ideas in a period of time. Employees can find this to be an unwelcome pressure, as it becomes increasingly difficult to find further scope for improvement. Some firms, especially Japanese-owned, conduct quality improvement sessions in the workers’ own time, which can lead to resentment unless there is appropriate recognition and reward for suggestions.
For Kaizen to be effective there has to be a culture of trust between staff and managers, supported by a democratic structure and a Theory Y view of employees. Good two-way communications and a de-layered organisation would also support this approach. Nevertheless, some workers might see the demands as an extra burden rather than an opportunity and it can take time to embed Kaizen successfully into an organisation’s culture.
You might also like
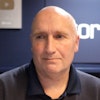
Leadership at Apple - Tim Cook's Quiet Cultural Revolution
22nd August 2013
What is Organisational Culture?
Study Notes
Handy's Model of Organisational Culture
Study Notes
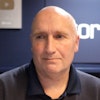
Leadership Lessons from the PepsiCo CEO
3rd August 2017
Netflix & Learn - The Minimalists
15th March 2019
Daily Email Updates
Subscribe to our daily digest and get the day’s content delivered fresh to your inbox every morning at 7am.
Signup for emails