Blog
Bring Him Home - UK Manufacturing Turns to Onshoring
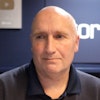
25th November 2013
A fascinating survey has been released by the UK's Manufacturing Advisory Service ("MAS"). It reports that a growing number of manufacturing SMEs are bringing production back to the UK from overseas. This is a process called "onshoring" which, of course, is the reverse process to "offshoring".
More than 15 per cent of SMEs either have or are in the process of bringing production back to Britain (onshoring), compared to just 4 per cent that have offshored production in the last year.
As illustrated in the chart above, the main reasons for reshoring production to the UK are to reduce cost (26 per cent), to improve quality (20 per cent) and to reduce lead times (18 per cent).
In the press release accompanying the report, Steven Barr, head of MAS explains that:
"It [onshoring] marks a major change in approach from five years ago, when the Far East and Eastern Europe seemed to be the destinations of choice. Buyers have realised that there is more to the ‘landing’ price than meets the eye, with delays in logistics and issues around quality adding a whole layer of hidden costs."
The survey suggests that there are more UK manufacturing SMEs onshoring now than there are SMEs offshoring. Of course, this net movement will vary from industry to industry. However, it is certainly an encouraging sign for those who wish to see a resurgence in UK manufacturing.
As we reported on the Business Blog recently, the process of onshoring has been particularly strong in the US where substantially lower energy costs have narrowed the production cost gap between the US and emerging economies like China and Vietnam.
The FT have picked up on the MAS survey and have provided some excellent additional interviews with relevant UK manufacturers who have analysed the relative attractiveness of manufacturing at home or abroad.
A good example they quote is Rotigrill, a supplier of rotisserie barbecues, who have chosen make the bulk of a new product for pubs and restaurants in the UK rather than China, using a local engineering company.
“When I looked at the cost and time involved in getting what is probably a low-volume product for China up and running through to the prototype stage, it was just ridiculous,” said Colin George, the company’s co-founder.
“Shipping costs have more or less doubled in 18 months – that is frightening. Wages in China are going up. We know that our cost is going to increase.”